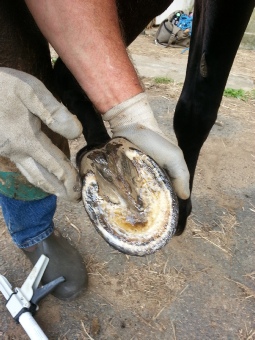
I’ve had numerous questions about Hoof Armor feeling sticky or tacky on the surface one or more minutes after application. I never answered that fully. My process has been to coat the hoof bottom with talc after applying Hoof Armor on concrete or rubber mats, so it doesn’t smear. Some people don’t like the hoof prints on the floor that they can never get off, and the talc helps with the tackiness. Applying Hoof Armor and putting the hoof down in either sand or soft dirt will also keep it from smearing until it cures.
So, now for the technical answer which I didn’t just make up. You can try it yourself and see. Any two-part adhesive formula is a complex calculation of a ratio of resin and curing agent. For instance it may be something like 3.75:1, or 4.15:1. If this is mixed perfectly, like in a laboratory setting, each part of resin will match up with an equivalent part of curing agent and there will be no parts of either left. However, in real life this seldom is possible. For one, the closest available dispenser ratio is a 4:1. They are typically available in 1:1, 4:1 or 10:1. The 1:1 ratio is considered the most “forgiving”, meaning the formula doesn’t have to be as accurate but that depends on the formula design. The one used for Hoof Armor is a 4:1 ratio which is the closest and most accurate mix available in the field.
The mix nozzles are also a factor. Hoof Armor uses the most efficient mix nozzles available, but every particle of Hoof Armor may not be mixed as accurately as if it were mixed by hand in a cup or container. However, because Hoof Armor cures so fast, mixing in a cup is not possible.
So, what happens is that the parts of Hoof Armor that match up…resin and curing agent…will cure very rapidly. Generally, all the curing agent is used up and there is a bit of resin left which didn’t find curing agent matches. This is the desired, recommended way of mixing, so that all the curing agent is used rather than having extra curing agent. Now, those parts that found matches will cure very rapidly while the unmatched parts (generally resin) will float on the top and stay uncured, or tacky/sticky. That’s what is noticeable…just the uncured resin on top whereas the rest underneath that has matched up is curing.
For every batch of Hoof Armor I mix I do a quality check from a random cartridge. Because the temperature in my lab varies, sometimes greatly, for consistency I warm the sample cartridge to around 80 degrees F. (putting a cartridge in your pocket for a bit will warm it to around 75 degrees F.) I put a 1” by 3” piece of cardboard on a paper towel. Then I dispense some Hoof Armor onto the paper towel to balance out the cartridge pistons and then I dispense a 2” bead of Hoof Armor on the cardboard and time how long it takes to set. After one minute I tap the bead with a used mix nozzle to see if it has set and is not runny. Generally, this bead has set up by this time although the top is still sometimes tacky. Although the adhesives manufacturer says to allow 24 hours for full cure, I add an accelerator to my formula which shortens that time to about 8 hours. After 8 hours even the top should not be tacky.
For anyone curious enough, this is an easy test to try themselves. I’ve found lately that, if the cartridge is warmed to around 80 degrees F, the surface of the cardboard doesn’t really affect the cure speed. Warmer than 80 degrees will not be faster than 80 degrees, though. I’m constantly trying to research and develop the best Hoof Armor and the best application techniques. Mostly, I learn from other people who use Hoof Armor in various situations. Thanks for that!